Of all the utilities we need for living on our property, power was the biggest project and took the longest. We began moving dirt for our solar array August 12 after our Temporary Power plans were approved, and turned our power on December 21.
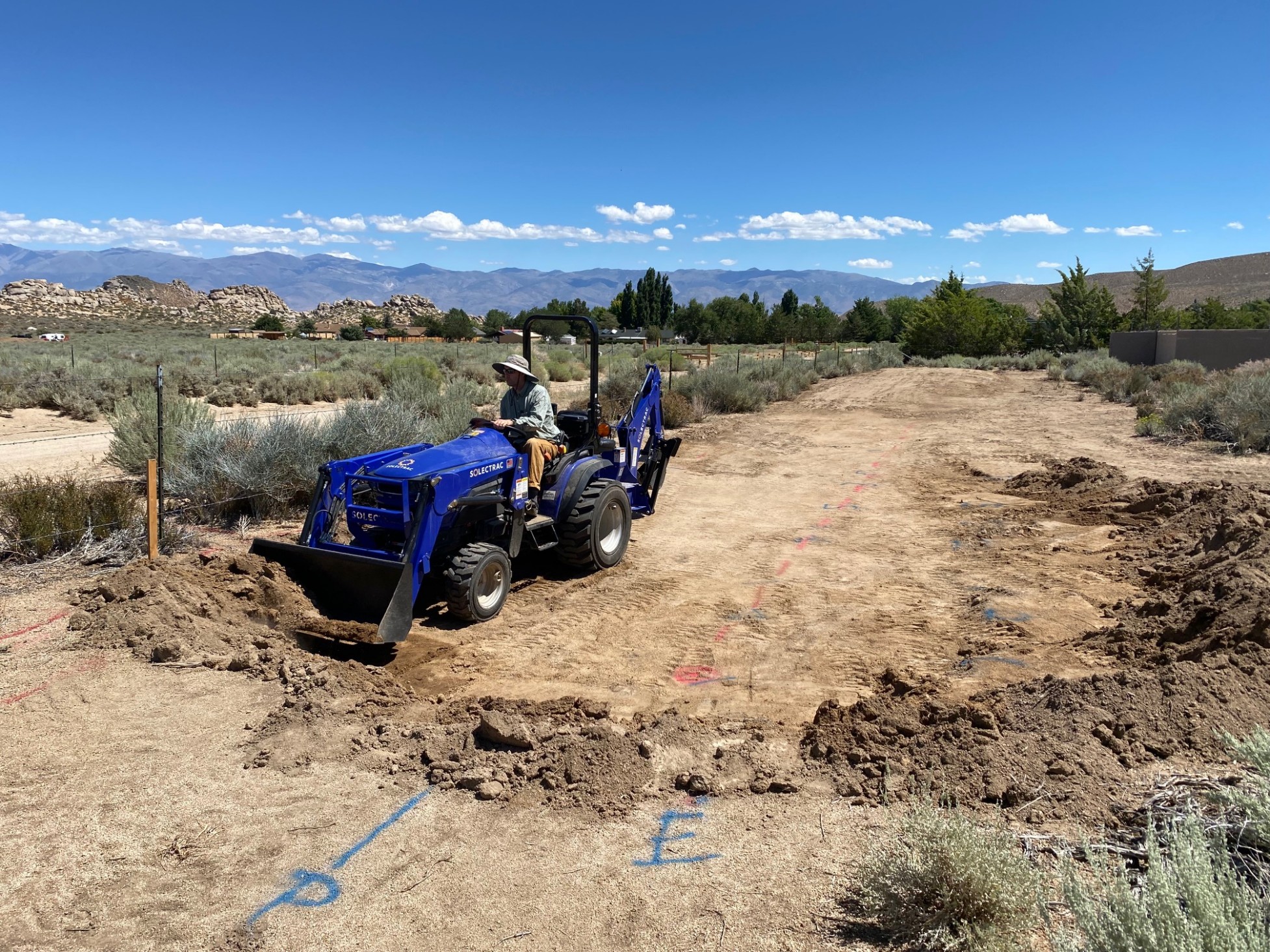
We began by grading the pad for the solar array. We’re going to be completely off grid, and, ideally, we’ll be all-electric on the Dome Base. If it hasn’t been clear from our electric cars, electric tractor, and electric tiny house, we’re working to limit our fossil fuel usage to the extreme minimum. Hence, a 29+ kW solar array, which translates to an area of 14′ x 112′. It shocks everyone who sees it, and most don’t even know that we’ve considered doubling it if we build the nerdy workshop of our our dreams and larger house someday.
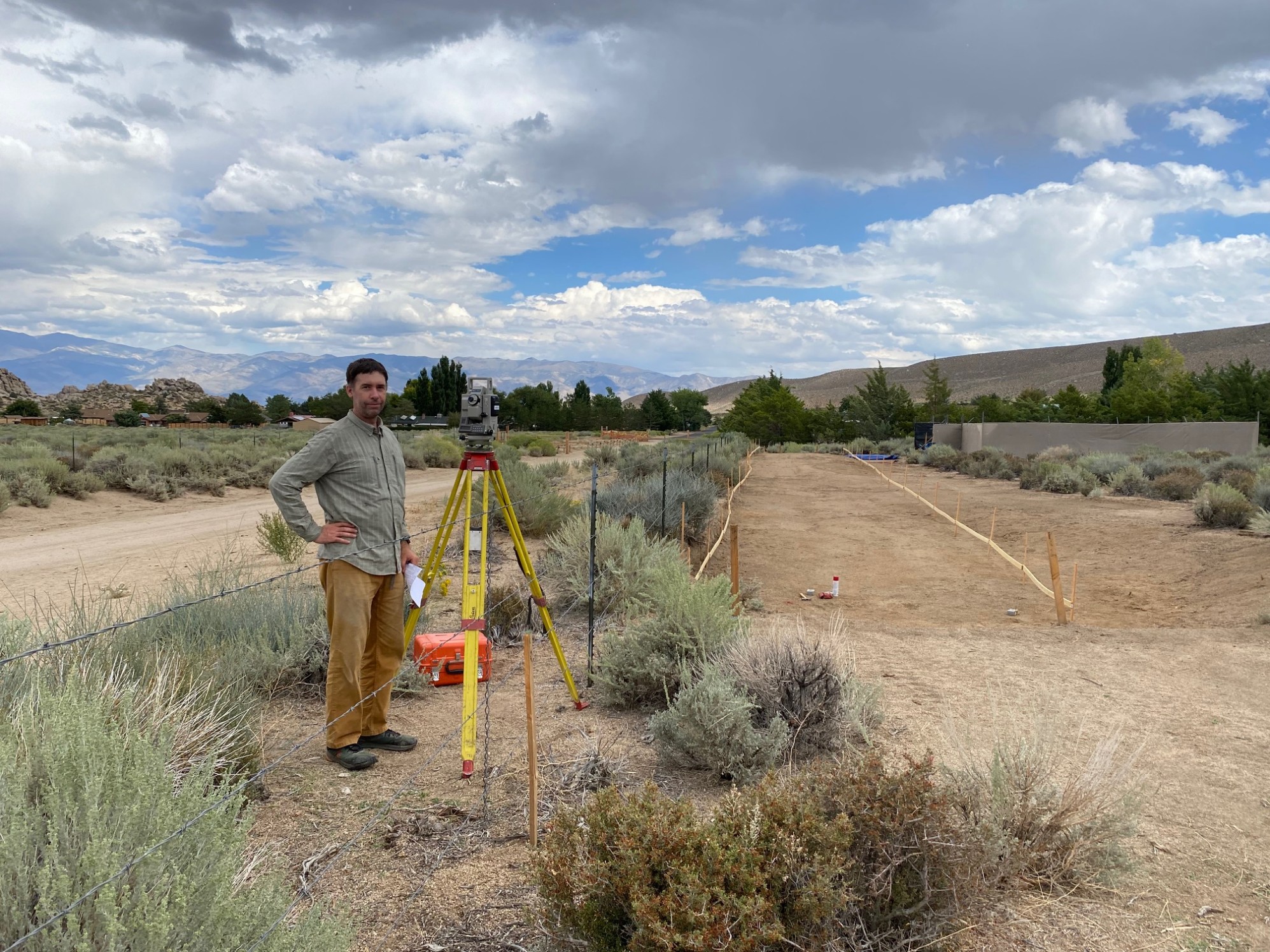
Our property slopes around 3% from west to east, so we used our tractor to level a long, east-west pad for the panels, which will face south at 30 degrees. It was a lot of dirt to move and compact. Our amazing neighbors up the hill let us charge Dipper from their solar array and loaned us a water tank and pump so we could wet the soil to get good compaction.
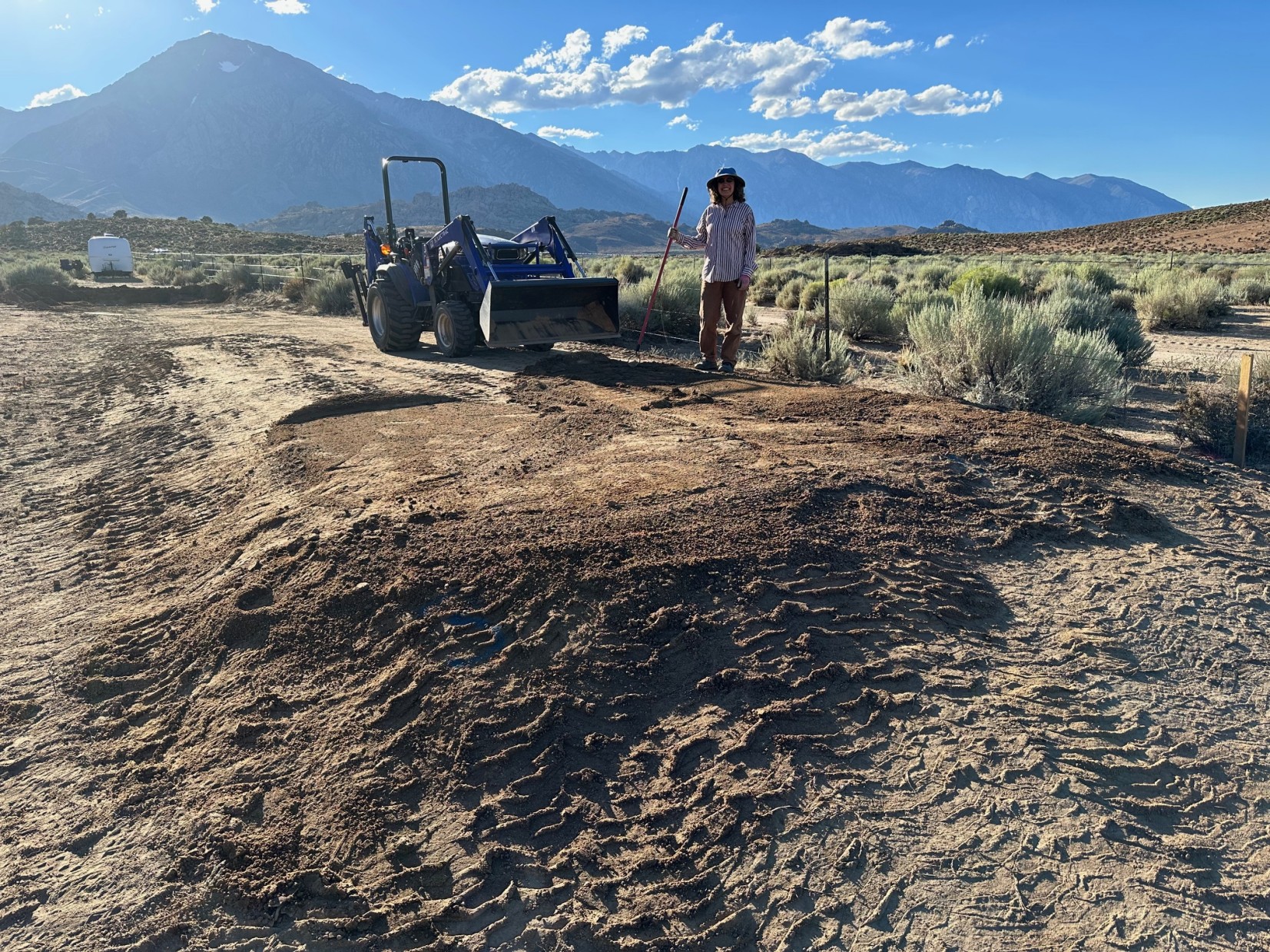
Eventually, the Utility Dome will house the complete set of batteries, inverters, and a monitoring station, but Jon designed a temporary power shed to hold 20kWh or 1/3 of the total batteries and 1 inverter. We built the shed at this time, which I lovingly refer to as the Bus Stop for, I think, an obvious reason.
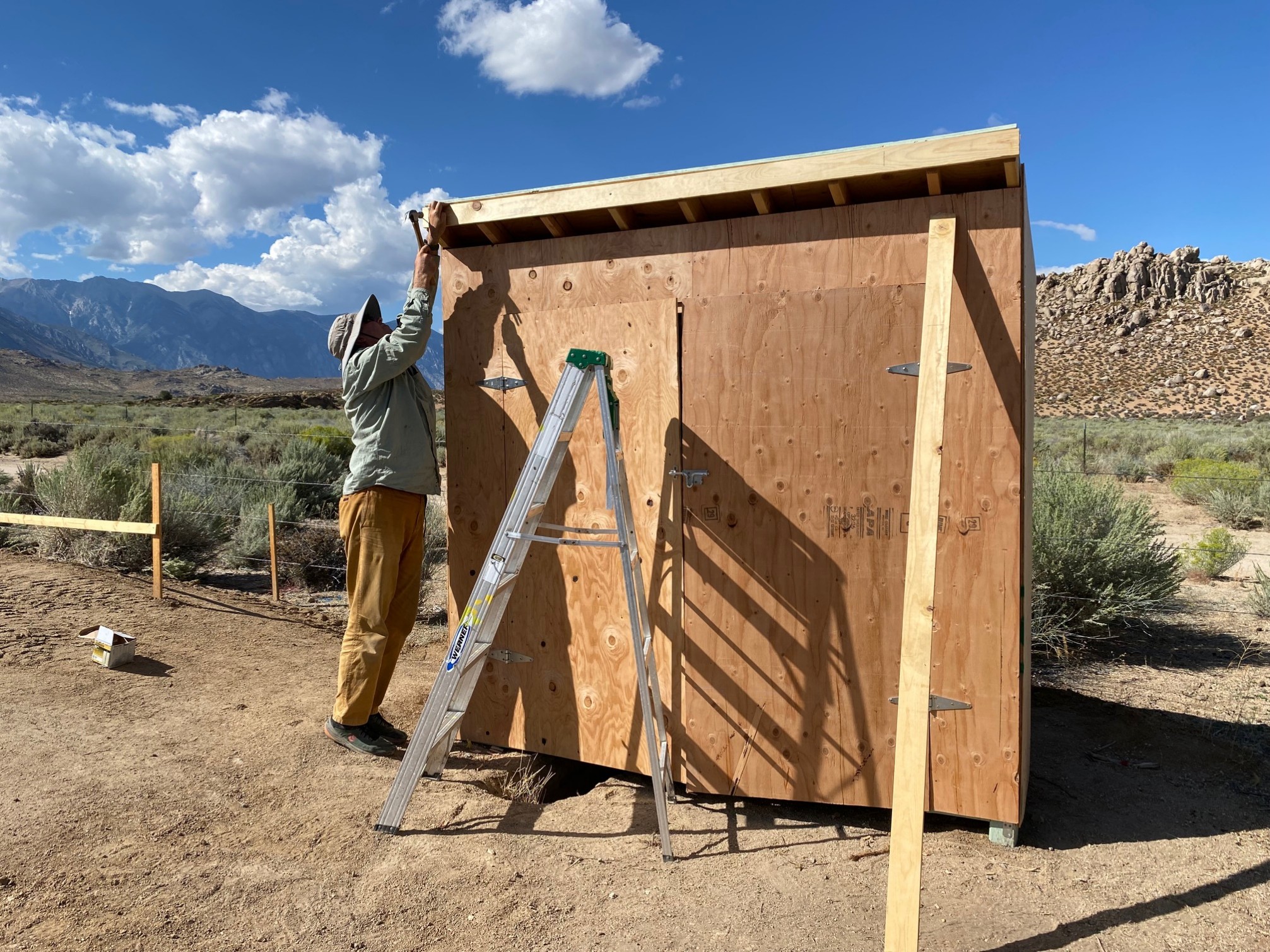
Then we were ready to dig the 72 holes for the concrete piers. We live in a high wind, high snow, seismic zone, so we require a beefy foundation. We could have had fewer holes with larger structural members, but we wanted to do it ourselves and were limited by the depth our little tractor’s post hole digger attachment could go. So we have 72 holes that are 16″ diameter and 4′ deep. We then covered the holes with filter fabric, so little creatures wouldn’t fall in and be stuck. We heart charismatic microfauna.
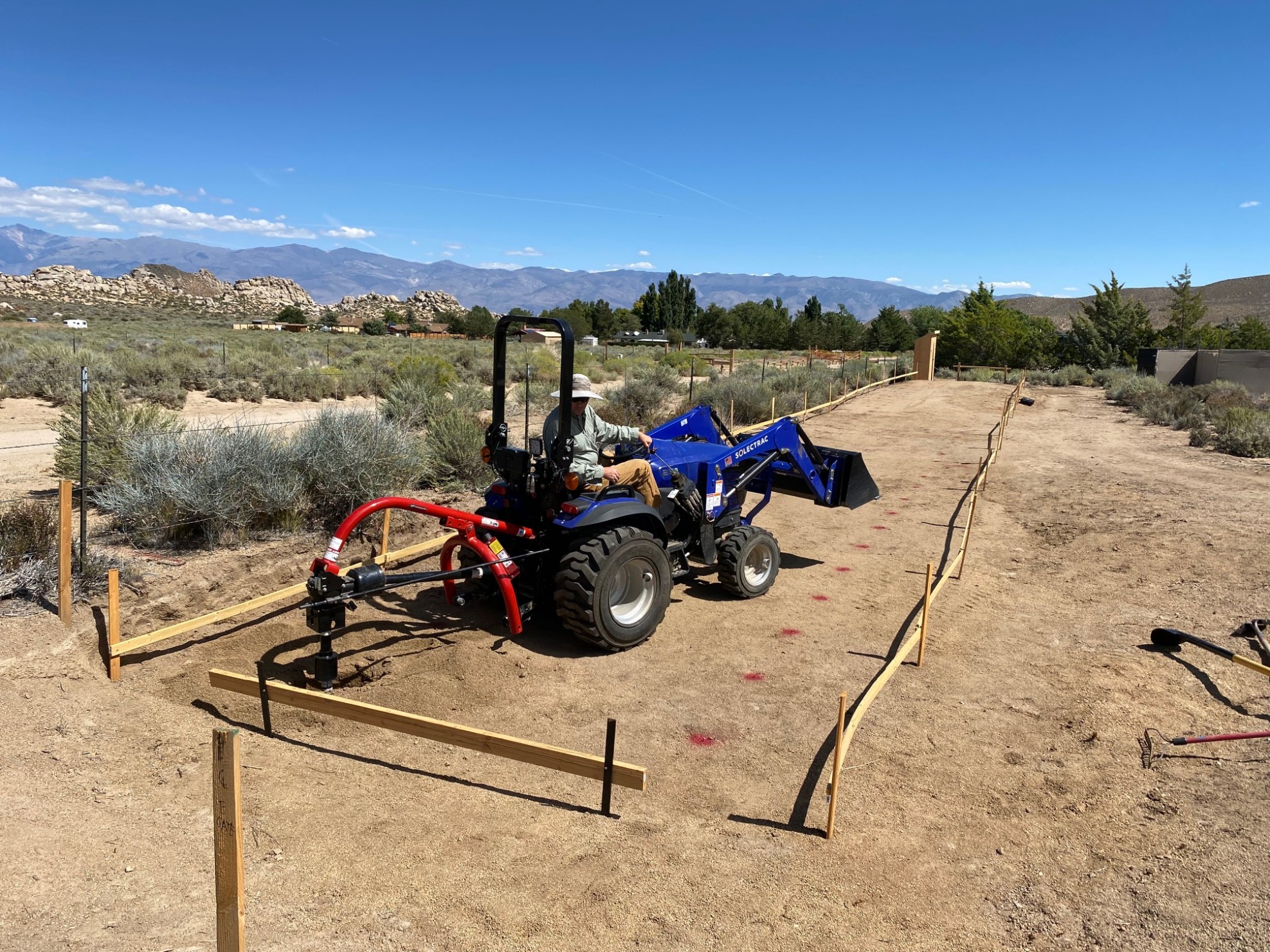
We were working on the pad when we got the ok to connect to the community water system, so switched gears for a few weeks.
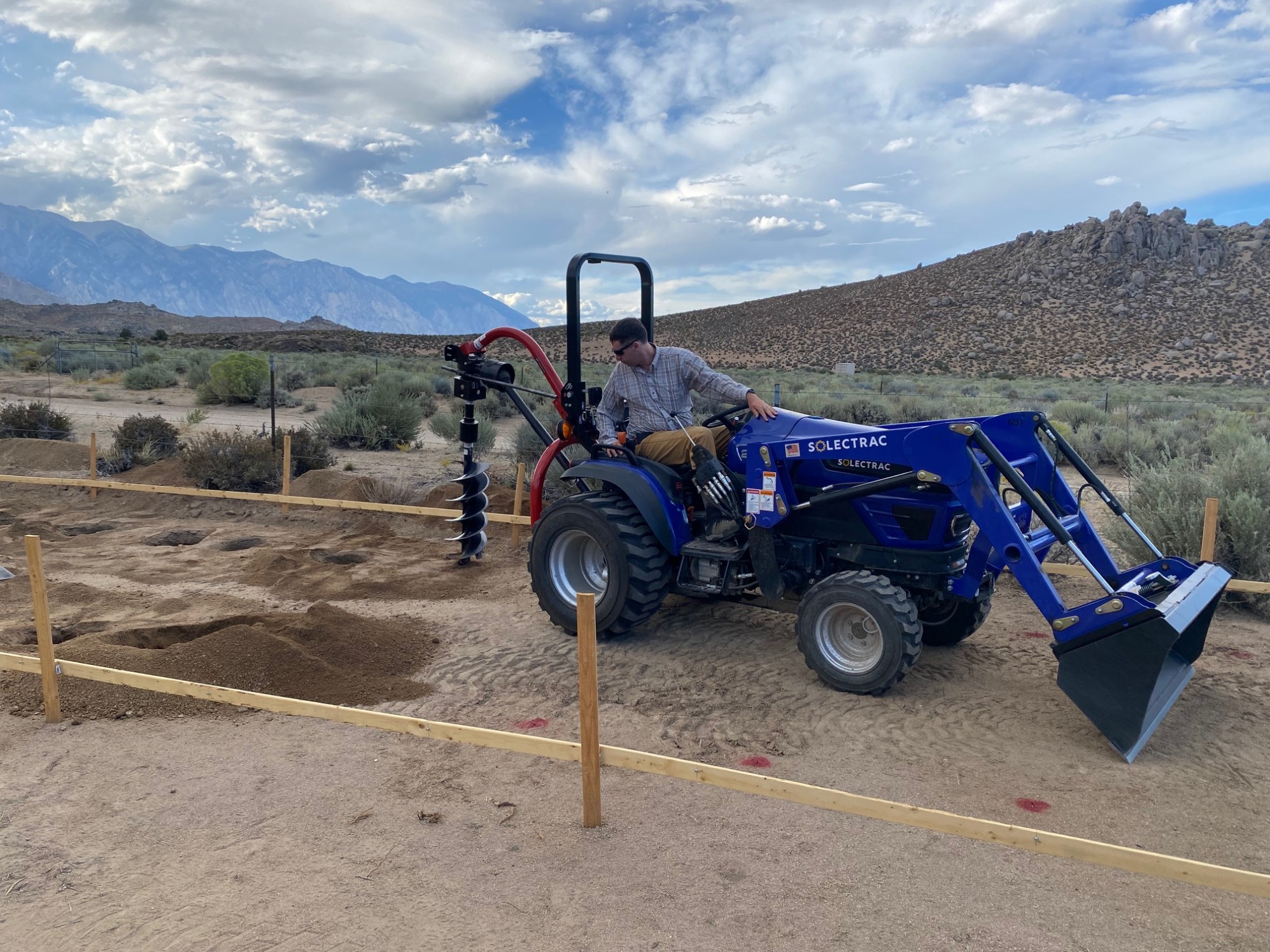
When we returned to our 72 holes, we still needed to clean them out with the spoon. The largest auger we could use was 12″, so we had to dig 2 holes for each pier. I don’t recommend that if it can be avoided. We also found that the auger had wandered on some of the holes (Dipper had developed a parking brake issue at the time), so we used the digging bar to expand some of the holes.
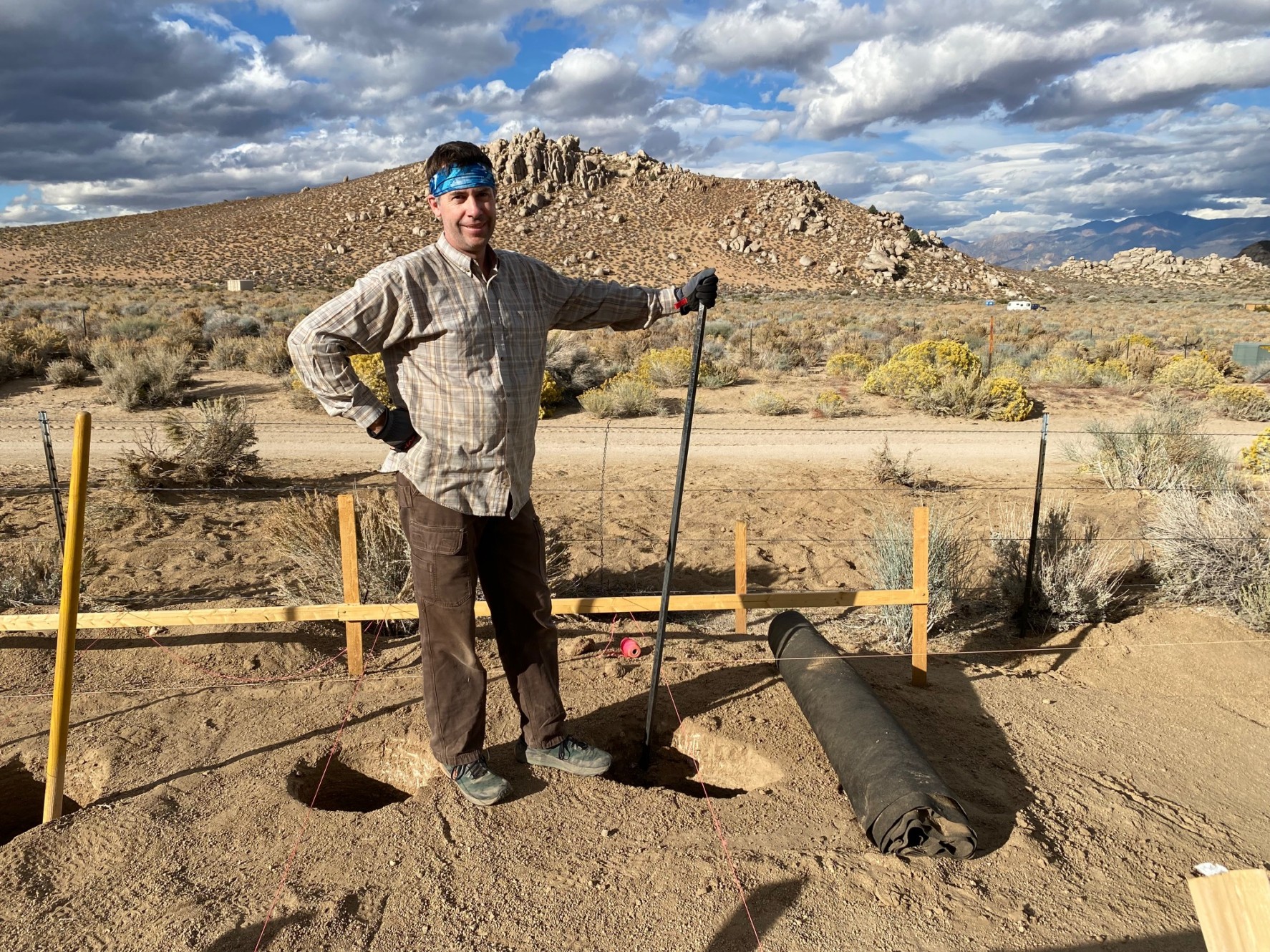
Time to construct the braces to hold up the tubing structure. We followed the instructions on Unbound Solar’s website, which were 2×4 Xs and plywood gussets. Unbound Solar caters to DIYers and they designed our system and sold us the components. The ground mount structural system is by Ironridge. Overall, I recommend both companies.
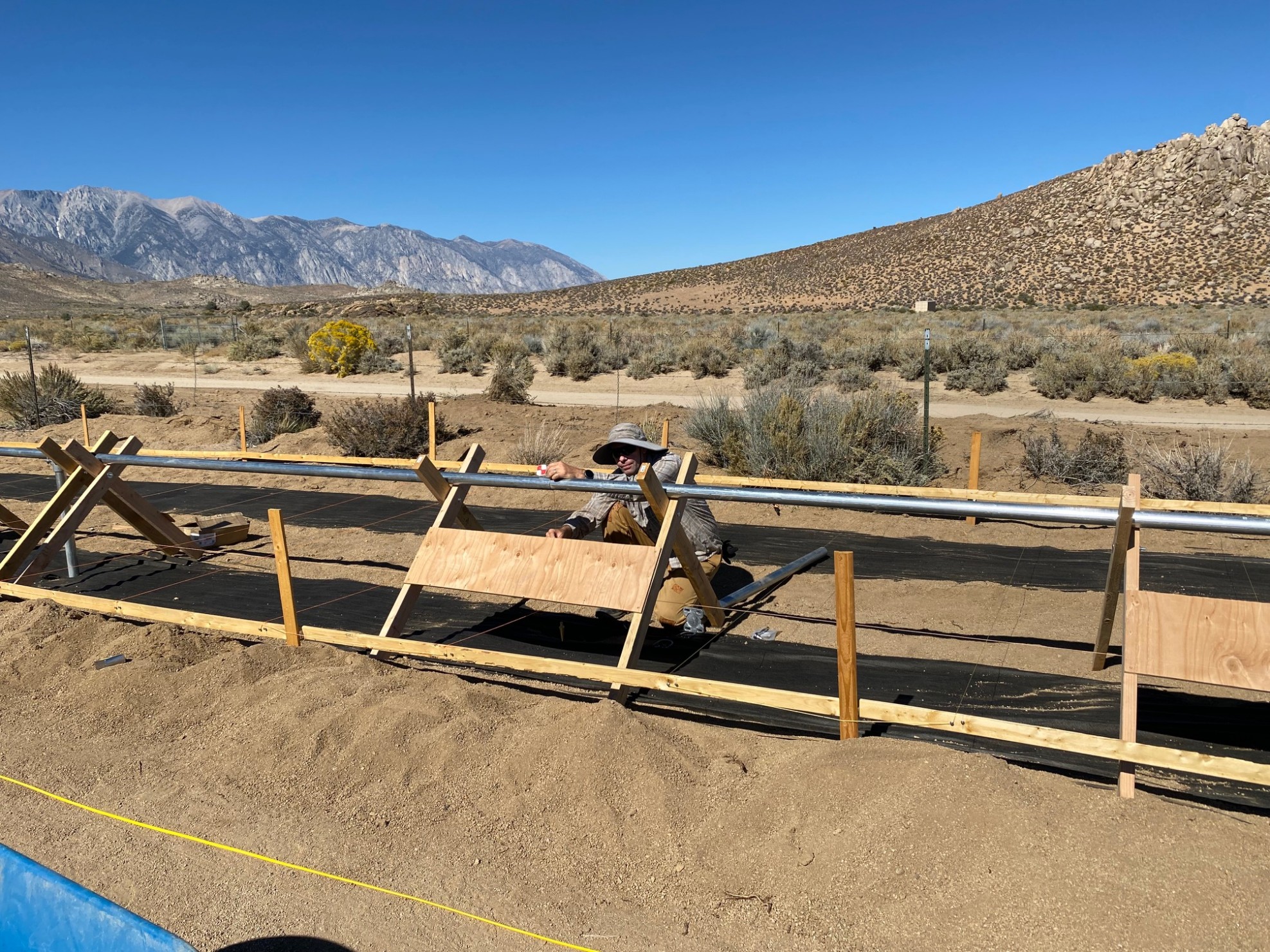
We could use 2″ pipe or mechanical tubing for the structure. We went with mechanical tubing. I drove my trailer down to the LA area one day to pick it up, and they cut the lengths for me, which was very handy. We installed and leveled the pipe, connecting the pieces with Ironridge components.
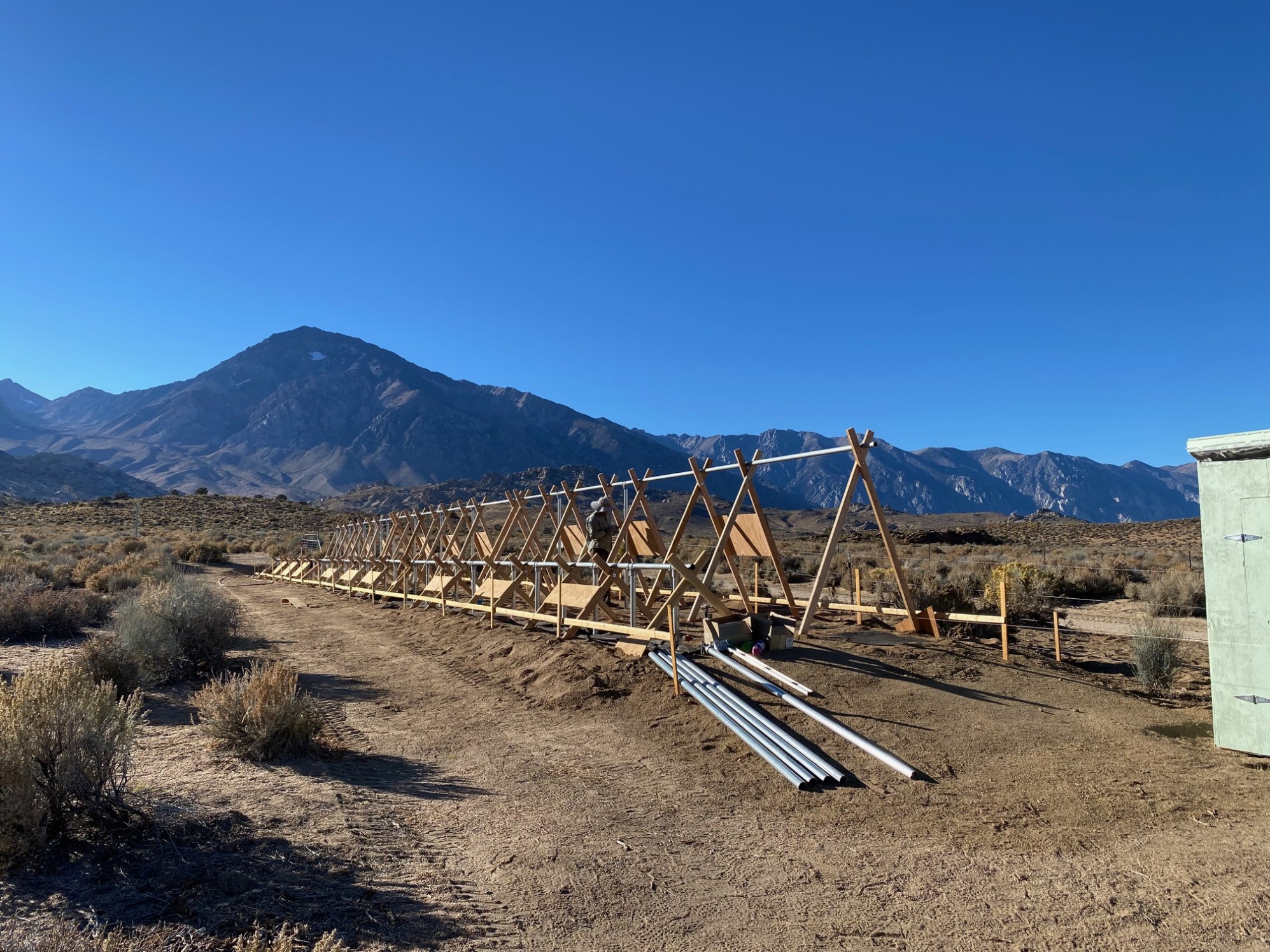
We enlisted help from a concrete pumper, who could park on the road and pump the concrete, Rick’s Special Pump Blend, over the fence and braces to our holes. In a very exciting morning, Jon handled the hose end of the pumper, filling holes, and I followed, churning the mud with a broom handle (my dad told me to do this to get the air bubbles out) and cleaning up hole tops with a shovel. Whew! We could have used a third person to help us that day, so now we know if we ever expand our array.
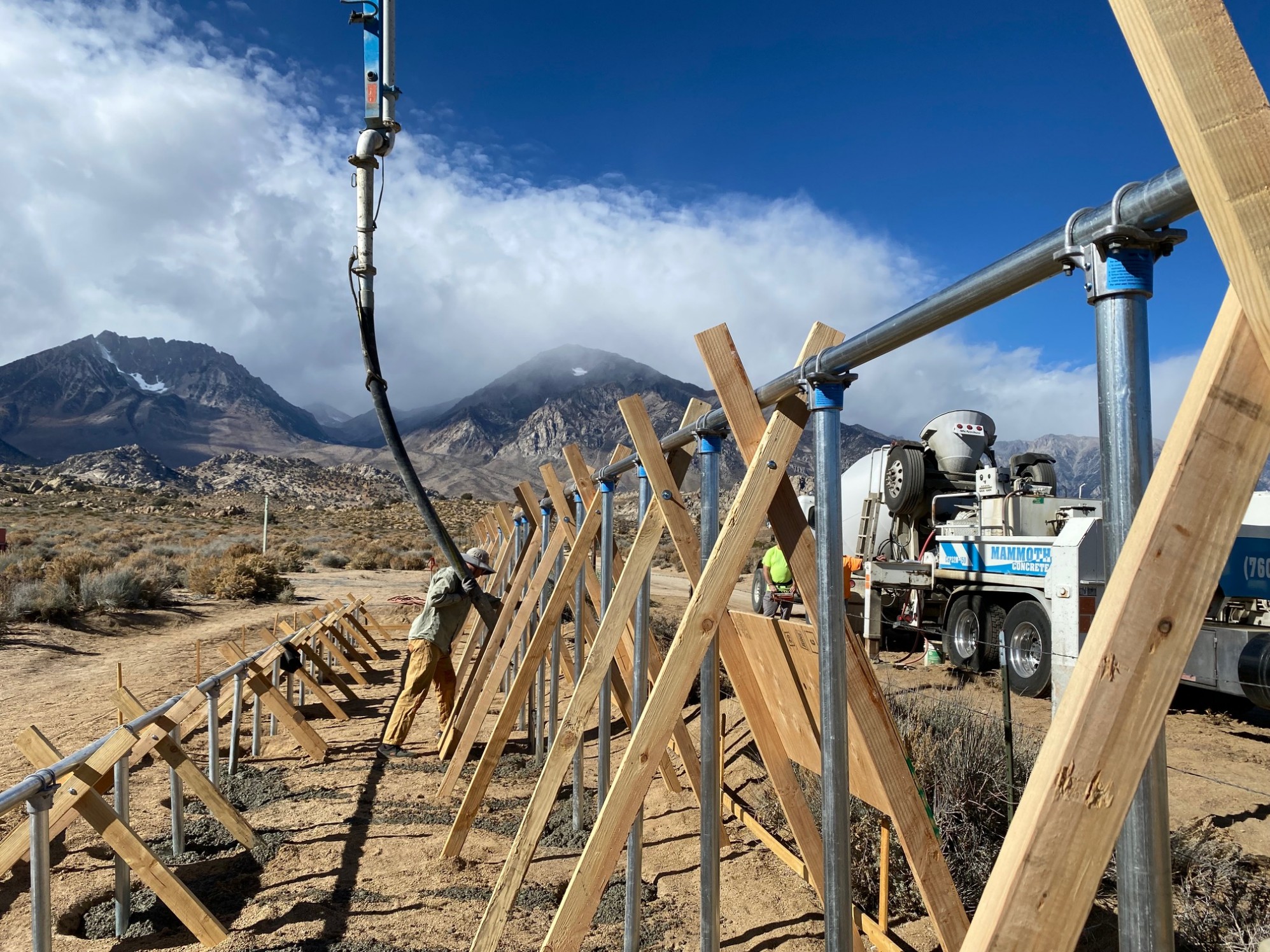
When the concrete cured, we began assembling the rest of the array structure, which was mostly lightweight rails that hold the panels up.
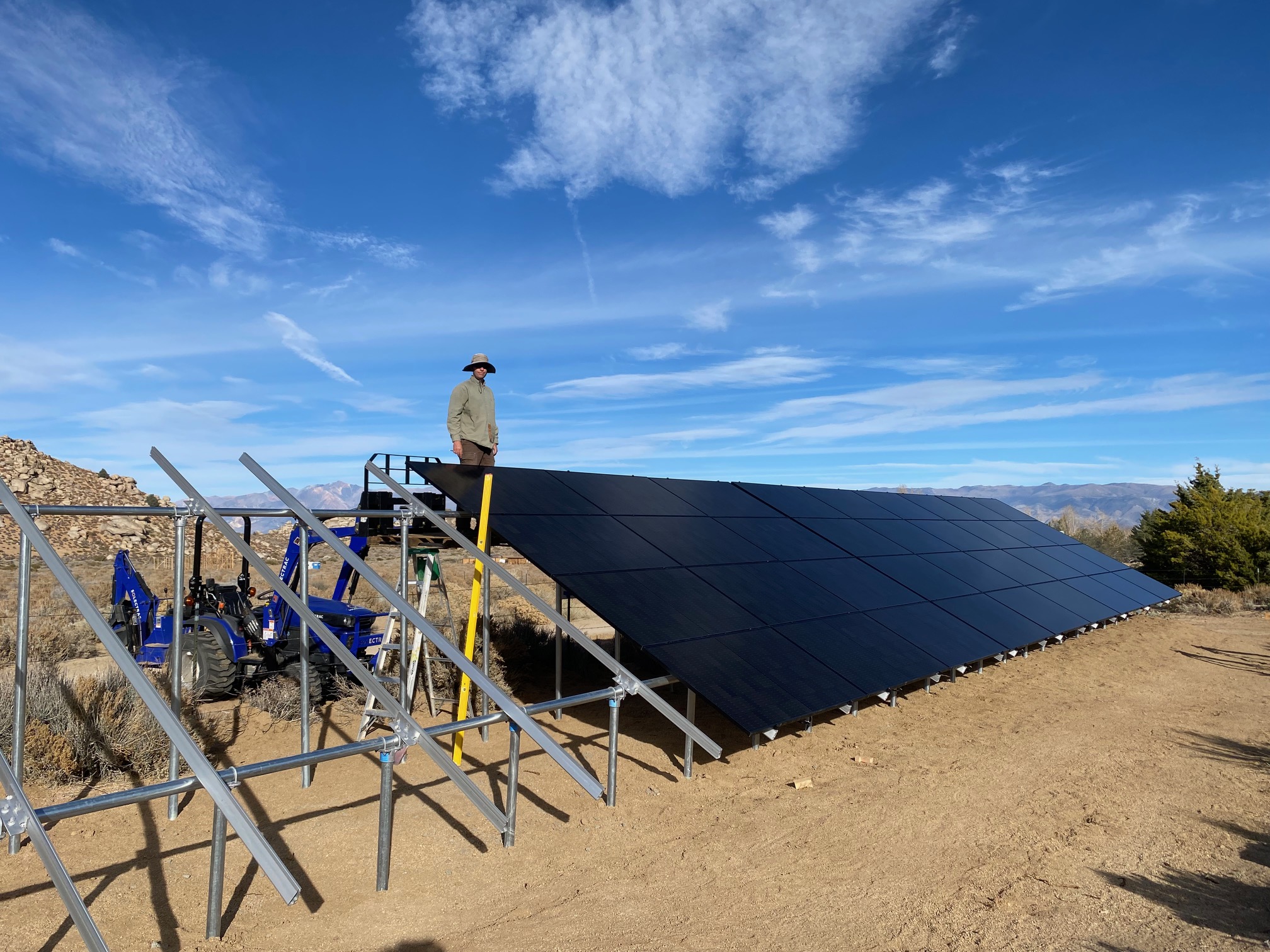
Around Thanksgiving, we installed all the panels. After we figured out the rhythm, it went pretty fast. Jon had to be the person who tightened many of the fasteners because he has a long enough reach and I don’t. For the back/highest row, Jon stood on a pallet lifted by Dipper and draped himself over the top to tighten fasteners.
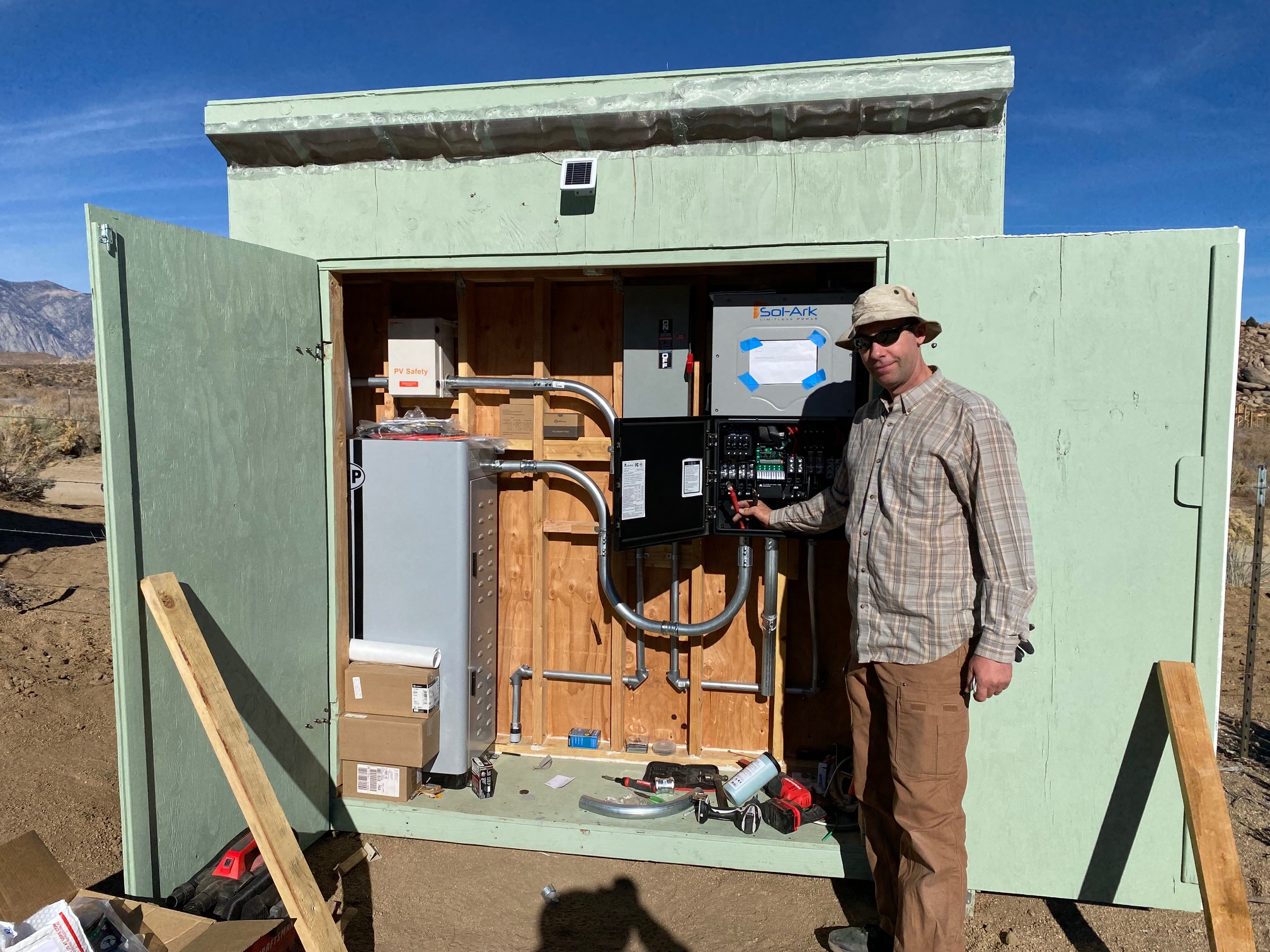
We next had a lot of wires to connect, heavy batteries, inverter, and cabinet to move into the Bus Stop. Jon did lots of wiring while I busied myself with the septic system.
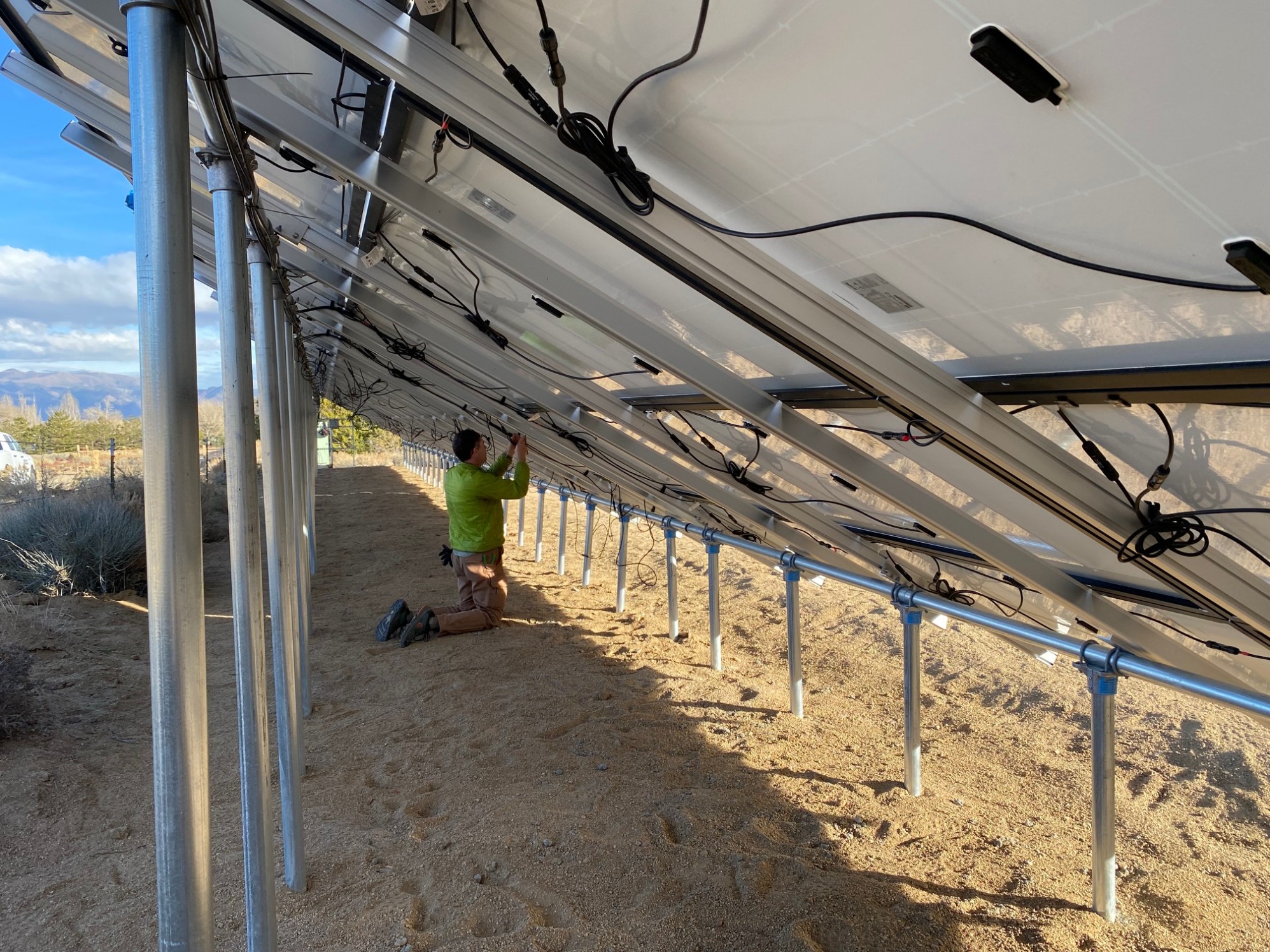
Back when we dug many trenches for water and drain lines, Jon also dug a trench for the electric conduit between the Bus Stop and the Temp Power panel.
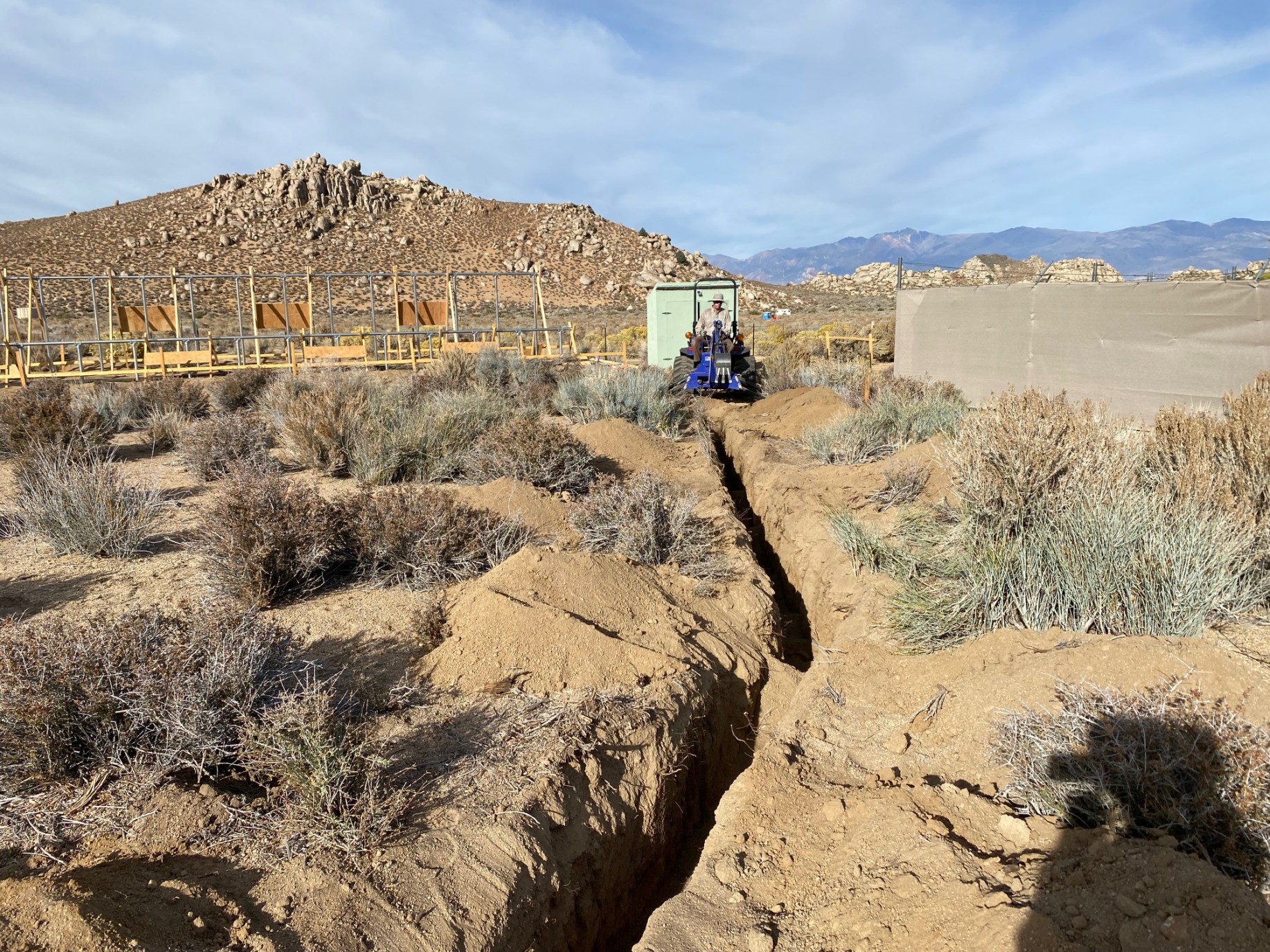
There was so much wire to pull through the conduit! Dipper held the spools. Jon did most of the pulling and I helped/tried to help by managing/trying to manage the unruly wires.
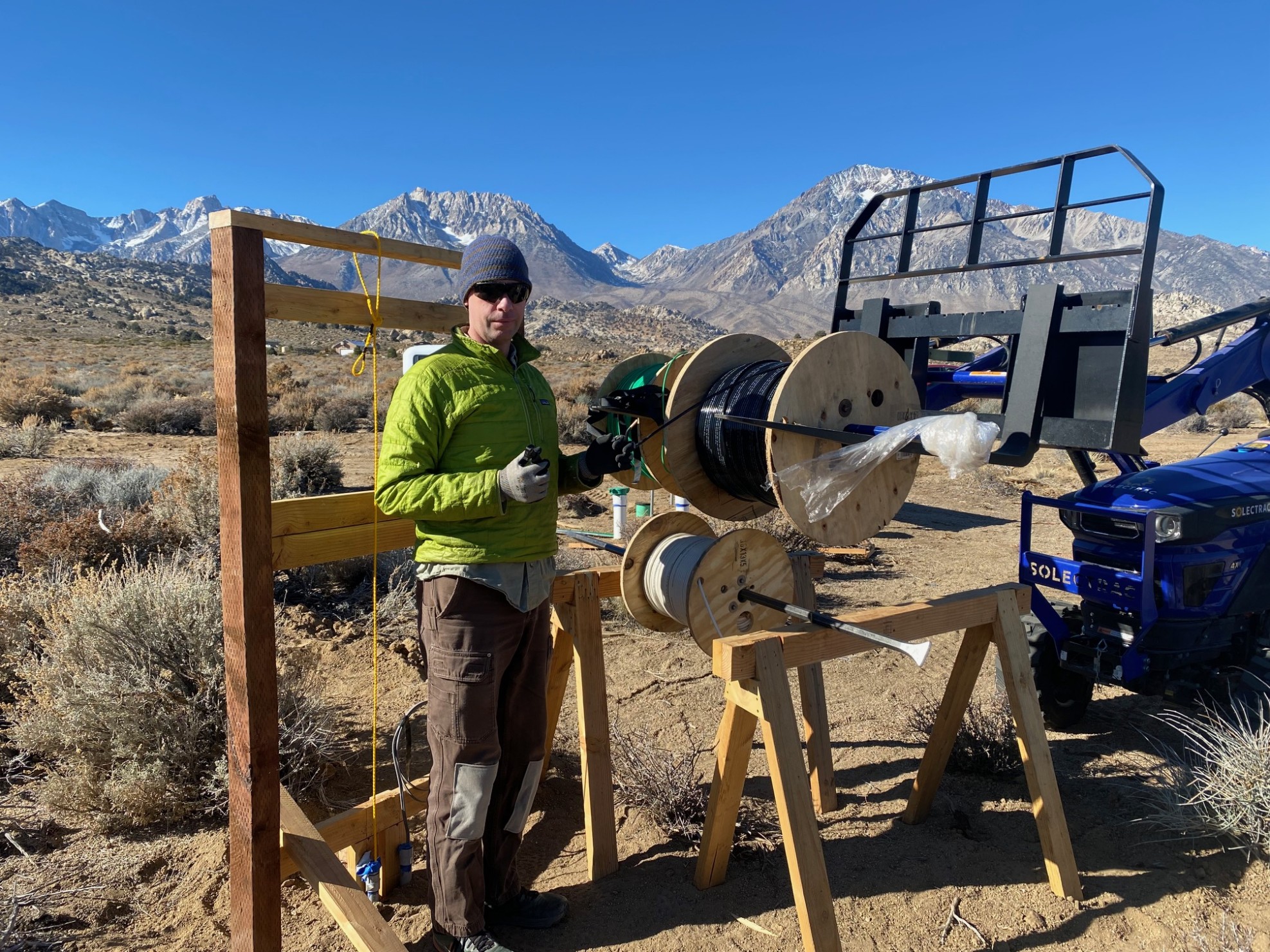
Jon did the magic that made our solar system work and power to begin flowing out of the receptacle outlets after our inspection on Dec 21. If you have any questions, he’s the best person to ask.
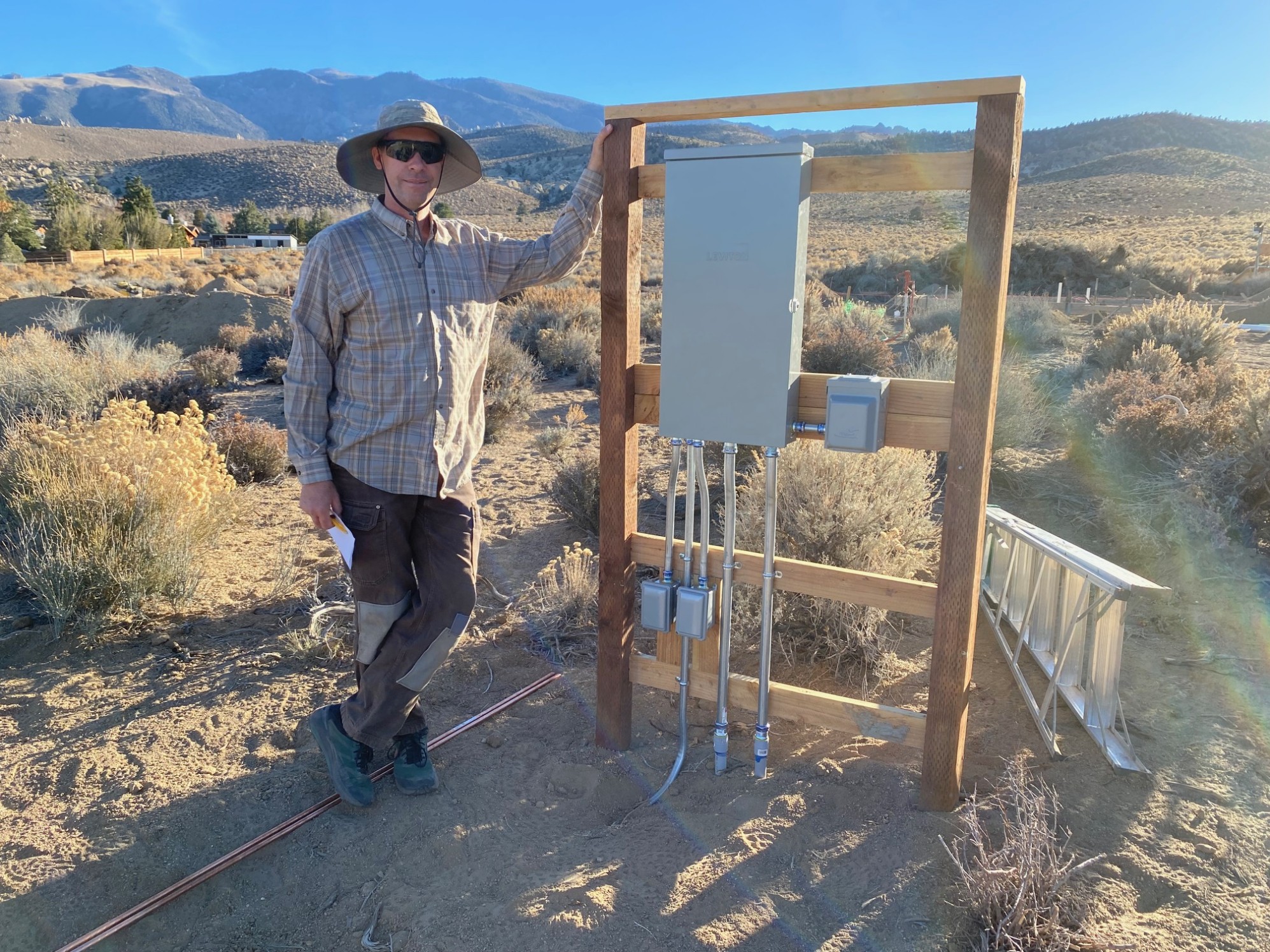